Sali
guitars enable high dynamic range of playing along
with natural timbre. The tone color, loudness and sustain
are well balanced in all registers. Due to their high
response Sali
guitars
can be
equipped with nylon strings which sound softly, naturally
and convincingly. This is more true also because of
carefully designed directional characteristic of guitar
body, which ensures optimal projection of the sound
towards the auditory.
Sali
guitars are finished with shellac and have
reinforced neck with carbon-fiber strips which prevent
deformations due to humidity and temperature variations.
In year 2014 we started to use truss rods in all our
models.
This enables fast, simple and elegant corrections
of eventual neck deformations. This means that playability of the instrument will not
change during the seasons, as well as over time in
general. The materials used for Sali guitars
are only of first or high quality. This ensures that both life time and
performance of the guitar are something on which you can
rely.
Resonant
frequencies of Sali guitars are engineered
in a way which results in highly consonant (pleasant)
sound. This is achieved by additional trimming of braces
or adding small masses at certain locations on a sound
board during the building process as well as once the
guitar is completed. Sali guitars
are special because
their frequency response is similar to the response
of a high-end guitar from
the simplified picture below.
One can see that the following is true for the resonant
frequencies of a high-end guitar in comparison to a
low-cost guitar:
-
Peaks are
relatively high for good guitars
-
The shape of
peaks is sharper for a good guitar in comparison to a bad
one
-
Peaks form
rather consonant than dissonant intervals (see our
"rule of consonance-dissonance")
(please note, that the
above explanation is stated highly simplified)
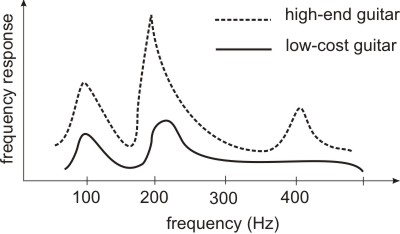
Traditional
procedures
Sali guitars are made by traditional procedures which
comprehend the use of hand tools and techniques for wood
working, finishing with shellac, etc. Skilled luthiers in the
past developed techniques for guitar building to the extreme
point and enormous details of their tradition are built
into our
high quality instruments.
We buy wood for our guitars on places with long tradition in
this business.
Our wood is naturally dried for at least 5 years in steady
conditions under our control before we use it in production
process. The quality of
wood is 1st grade or high
grade. We use the following types:
-
spruce or cedar for soundboards
-
mahogany (khaya, sapeli), cedar for necks
-
Indian rosewood or flame maple for backs and sides
-
ebony for fingerboards
-
rosewood for bridges
Handmade
All Sali guitars are hand made.
We spend approximately 150 hours on each instrument.
However it usually lasts 5 months in order to complete one
guitar. This is due to time-demanding finishing with French
polish (if demanded by a customer) and all necessary adjustments of
both saddles, fretboard, etc. once the guitar is finished.
Each instrument is an
unique product, usually made for a known customer. Because one
guitar is treated by only one pair of hands and eyes, we are
able to control all phases of work. Our approach ensures
quality and we trade this quality for your security with
pleasure.
Precision
Precision of guitar making does not affect only its appearance
but also its sound. We are carefully focused into perfect matching
between different parts. This enables thin layers of glue, thus your
Sali guitar will vibrate without any unnecessary loses
of sound.
Very important part of a guitar is its neck with fingerboard.
Sali
guitar has a reinforced neck which prevents
undesirable deformations due to string tension on one side,
and humidity and temperature changes on another side. The neck
reinforcement is performed with carbon-fiber strips which are
extremely light and strong, thus your Sali guitar will
be a joy in your hands. A two-way truss rod enables quick and accurate
neck adjustment if necessary.
We can achieve so desired low string action at all
frets because the neck relief of Sali guitars is
calculated with engineering precision and worked with
accuracy. Consequently the playability of our guitars is
something which enraptures.
Science behind Sali guitars
Several years of different
researches performed at Faculty of
Mechanical Engineering in Ljubljana and later in Samo Sali's
workshop enable that Sali guitars are well balanced
combination of tradition, hand making, precision and
science.
The influence of
machining process on the acoustic properties of guitar
The wood tissue in any tree mainly consists of cells which are
parallel to the tree's stem. These cells are sensitive to
deformations which always occur during hand working or
machining with machine tools of any wooden workpiece. Samo Sali defined the influence of planing,
sanding and milling on the acoustic properties of wooden
resonant boards. In planing the way of cutting the wood cells
is different than in sanding and milling, and consequently
each cutting process affects acoustics of a thin wooden board
in a different way. All these findings are encountered in
process of making Sali guitars.
-
KOPAC
Janez, SALI Samo. The
frequency response of differently machined wooden boards.
J. Sound Vib.,
1999, vol. 227, no. 2., p. 259-269
(PDF, 329 kB)
-
SALI
Samo, KOPAC Janez. The
influence of different machining processes on the acoustic
properties of wooden resonant boards.
CAS j.,
1998, vol. 3, no. 5, series II, p. 15-21
(PDF, 489 kB)
Rule of consonance - dissonance
Each guitar tone has its spectrum. A sample spectrum of empty
1st string is shown in figure below. The tone spectrum shows
us which frequencies (i.e., frequency components) are
contained in the plucked tone and how strong they are. There
is certain music theory which says that some combinations of
tones are pleasant (consonant) and another ones are unpleasant
(dissonant) to the human ear. We can apply this
theory for a situation within any guitar tone. Some
combinations of frequency components inside the tone are
consonant and another one are dissonant. In well-sounding
guitars the portion of consonant combinations of frequency
components is large, and portion of dissonant combinations of
frequency components is small in comparison to
low-quality guitars.
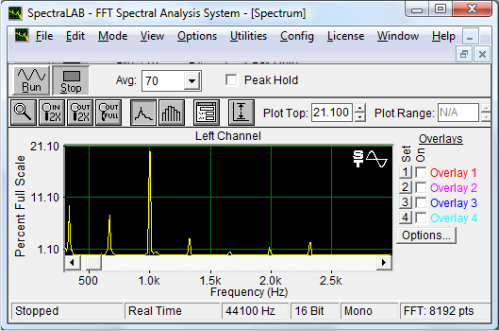
Frequency response
of the sound
board
The most important part of a guitar is its sound board. Due to
non-homogeneity of wood, which means that density of wood
tissue varies over the board, the acoustic properties of each
wooden board in nature are different. Each sound board has certain number of wooden reinforcements
(called braces and fans) and we are able to calculate
their locations. Some
places on a sound board are highly inappropriate for gluing the
braces because they can block vibrations. In contrast, some
places are ideal for brace gluing because adding the mass and
stiffness at right locations can increase acoustic response of
the board. Due to already mentioned non-homogeneity of wood
the appropriate and inappropriate places for braces and fans
are different for different sound boards. Adequate measurements and methods for calculation of optimal
position of braces and fans enable beautiful sound of our
guitars. To implement these methods some
braces and fans must be curved with accuracy about 1 mm before
gluing onto the soundboard.
Measurements of
sound board
The luthiers in the past (e.g., Amati, Stradivari, etc.)
developed a method named "tap toning" by which they
established the response characteristics of the board. We
developed an expert system for measuring the response of
guitar sound boards. This system enables us to predict which
frequencies in any tone spectrum of the finished guitar will
be emphasized and which ones will be diminished.
Guitar tone depends much on
sound board
"Tap-toning" method can be
modified in order to produce a high-end quality guitar. Namely,
under certain circumstances we can tap the sound board only at
a specific location although its response will be
characteristic for a whole sound board. In addition, we
found out that tonal characteristics of the guitar can be
correlated with characteristics of certain range of guitar's
frequency response.
Tone improvement
According to the board's response the luthiers in the past
performed additional removing of wood at certain locations to
achieve optimal response which means loud and pleasant sound.
Sometimes it is necessary to perform additional corrections
for a completed guitar as well. If so, we rely on a method
which enables these corrections by removing the wood through the sound hole.
Pictorial overview of
making guitars |